ホンダのタイにおける四輪車生産販売現地法人であるホンダオートモービル(タイランド)カンパニー・リミテッド(以下、HATC)は、タイ・プラチンブリ県・ロジャーナ工業団地内に完成した新四輪車工場のオープニングセレモニーを5月12日に挙行しました。
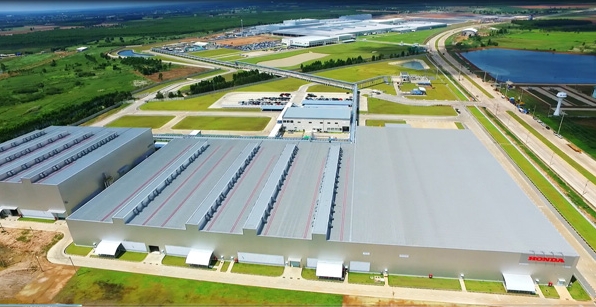
今回の新プラチンブリ工場は年12万台の生産能力があり、これを加えてHATCは年42万台の生産体制を持つことになります。
新プラチンブリ工場には、四輪完成車の量産では世界初(ホンダ調べ)となる、完成車組立のメインラインに組み込まれる流動型のセル生産方式ライン「ARC(アーク)ライン」(ARC:Assembly Revolution Cell)が設置されています。
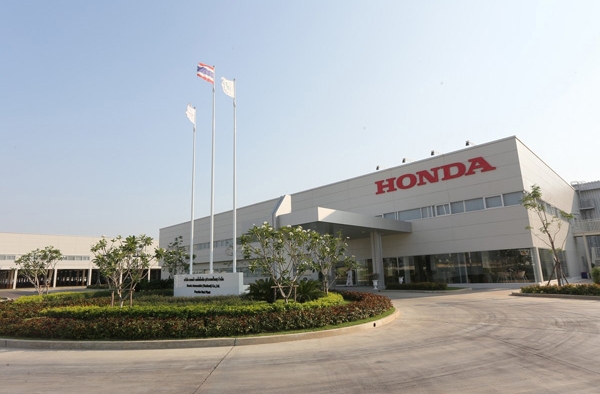
新プラチンブリ工場では、昨年の10月に樹脂工場が、今年2月にエンジン工場が稼働を開始し、今年3月から新型「CIVIC(シビック)」の量産を開始しています。
ホンダでは、今後も小型車を中心に生産モデルを増やし、タイの国内市場ならびに輸出における競争力を強化していたい、としています。
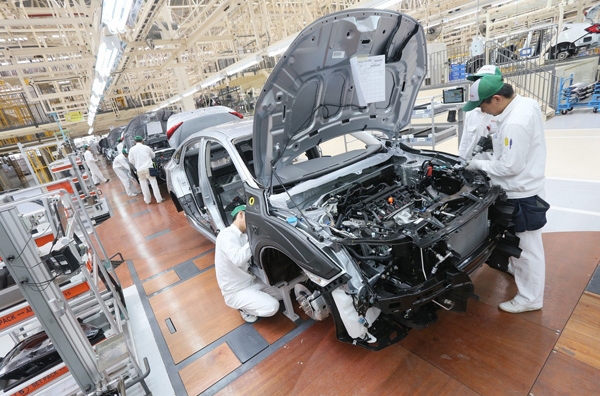
ホンダのタイ工場というと、思い出すのが2011年11月に発生した大雨による洪水での浸水。
当時「浸水した新車が販売されるのでは」という噂を打ち消すために、被災したタイ工場の全生産車を廃棄処分したことが記憶に残っています。
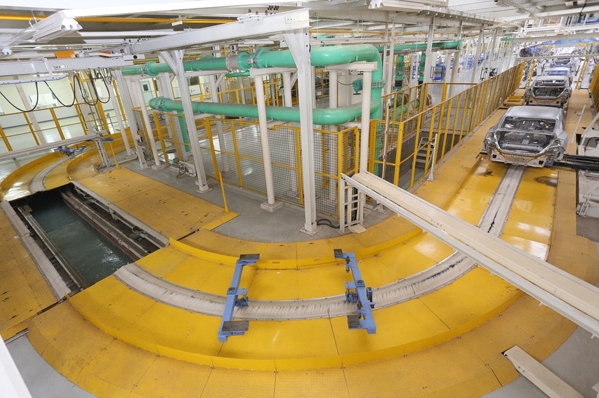
ホンダは、洪水に見舞われたロジャーナ工業団地内で洪水後の2013年から今回の新プラチンブリ工場の建設を開始しており、同工場の完成はホンダが5年前の洪水被害を乗り越えた証といえます。
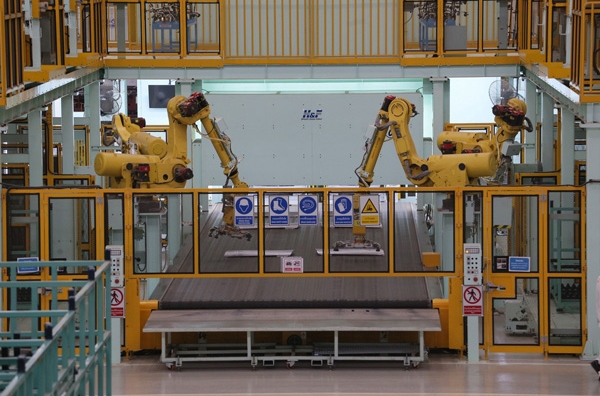
新プラチンブリ工場の完成式典に招待されたタイ政府副首相ソムキット・チャトゥシピタック氏は次のようにコメントしました。
「自動車産業はタイ経済の発展にとって大変重要であり、ホンダがタイを戦略的な生産および輸出拠点として位置づけ、環境に配慮した先進的な技術を投入することを歓迎します。グローバルにおける四輪車生産拠点として、タイの位置付けがますます強化されるものと期待しています」
同式典でのホンダ代表取締役社長 社長執行役員 八郷隆弘氏のコメントは次の通りです。
「タイは、国内市場のみならず、グローバルでの販売拡大を牽引するアセアン市場を含む全世界へ完成車および部品を供給することで、ホンダの生産拠点の一つとしてその存在感を高めてきました。ホンダの最新の生産技術を最大限に活用するこの新プラチンブリ工場の完成にともない、タイの役割をこれまで以上に価値のあるものにしていきます」
同じくホンダ執行役員 アジア・大洋州本部長 安部典明氏は次のようにコメントしました。
「この新工場における最新で高効率の生産技術により、ホンダの商品はさらに競争力を高めていきます。シビックに加え、将来はここプラチンブリ工場で生産する小型車モデルを増やし、タイ市場ならびに輸出向けの競争力を強化することで、タイの経済に貢献していきます」
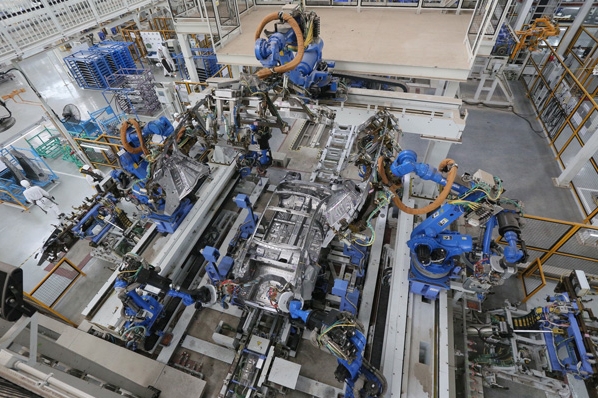
ホンダのタイ・新プラチンブリ工場には次のような技術が採用されています。
[生産効率向上]
組立ライン:世界初(ホンダ調べ)となるARC(Assembly Revolution Cell)ライン
→生産効率を従来の製造工程比で約10%向上
プレス:サーボ制御、高速フィーダー採用
→プレス工程の効率を従来比で25%向上
溶接:軽量小型ロボット治具の採用
→溶接ロボット稼働率を40%向上
[人・環境に配慮した取り組み]
溶接:生産工程で使用された冷却水を再利用する「水搬送」を採用
→施設管理:屋根から自然光を取り込んだ「スカイライトルーフ」の採用
(山内 博・画像:ホンダ)
【関連記事】
世界初!ホンダが新発想の量産完成車組立ライン「ARCライン」をタイ工場に導入
http://clicccar.com/2016/04/25/367879/